TARGHE IN PRESSOFUSIONE
L’impatto del rilievo
Una targa in pressofusione risponde a specifiche esigenze tecniche ed estetiche relative alla personalizzazione… In una parola: rilievo! Nonostante la presenza di altre tecnologie di lavorazione da noi fornite permettano di sviluppare elementi di rilievo con materiali metallici, come ad esempio l’incisione chimica, di fatto quando abbiamo bisogno di targhe personalizzate con degli elementi più complessi a livello di tridimensionalità e di colore, la scelta di targhette in pressofusione è la soluzione migliore.
Vediamo come avviene l’intero processo produttivo
per capirne meglio vantaggi e svantaggi.
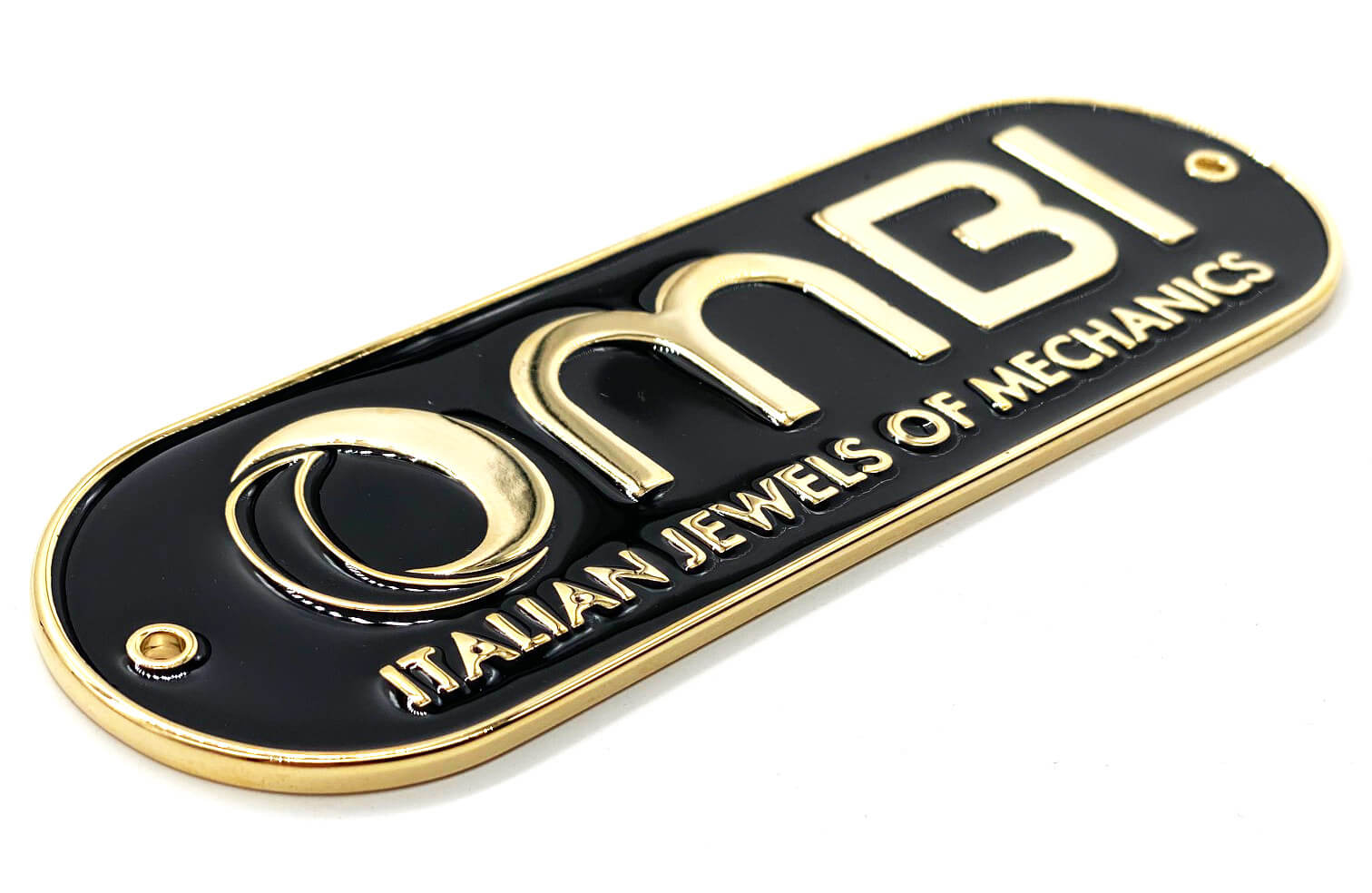
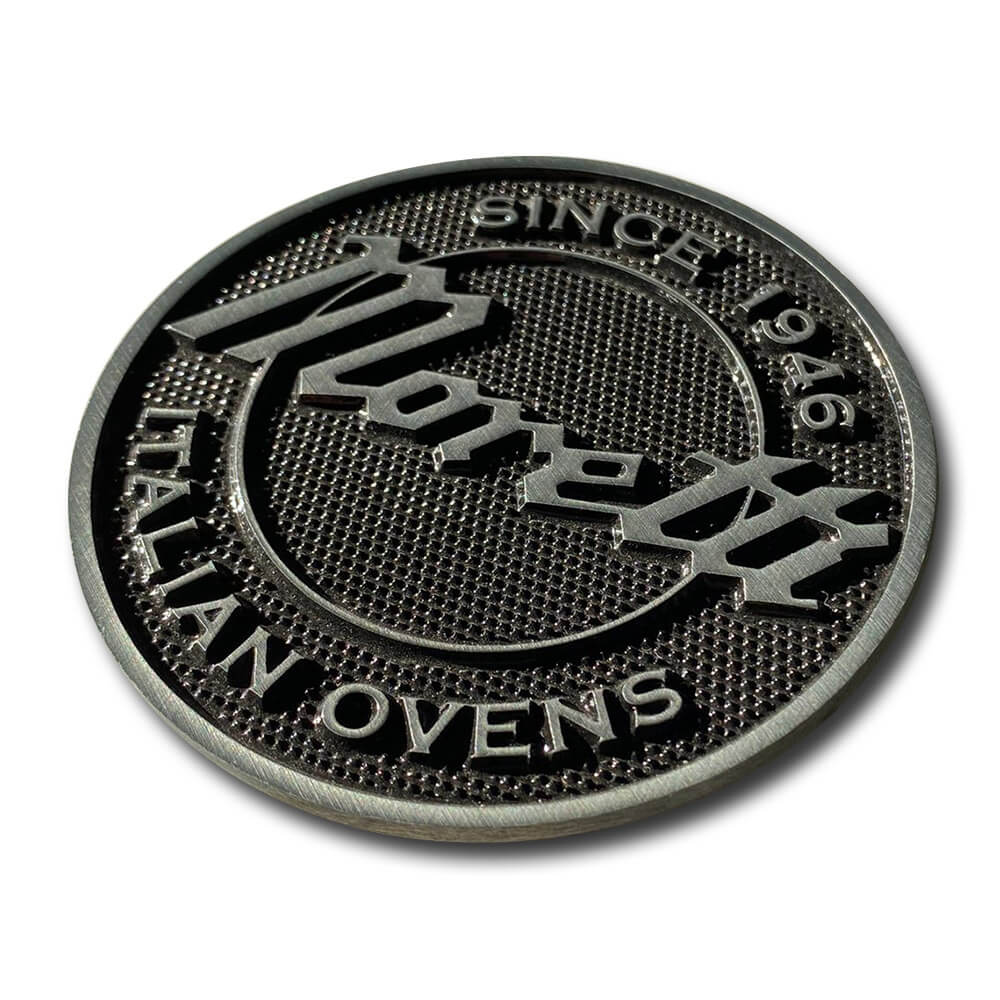
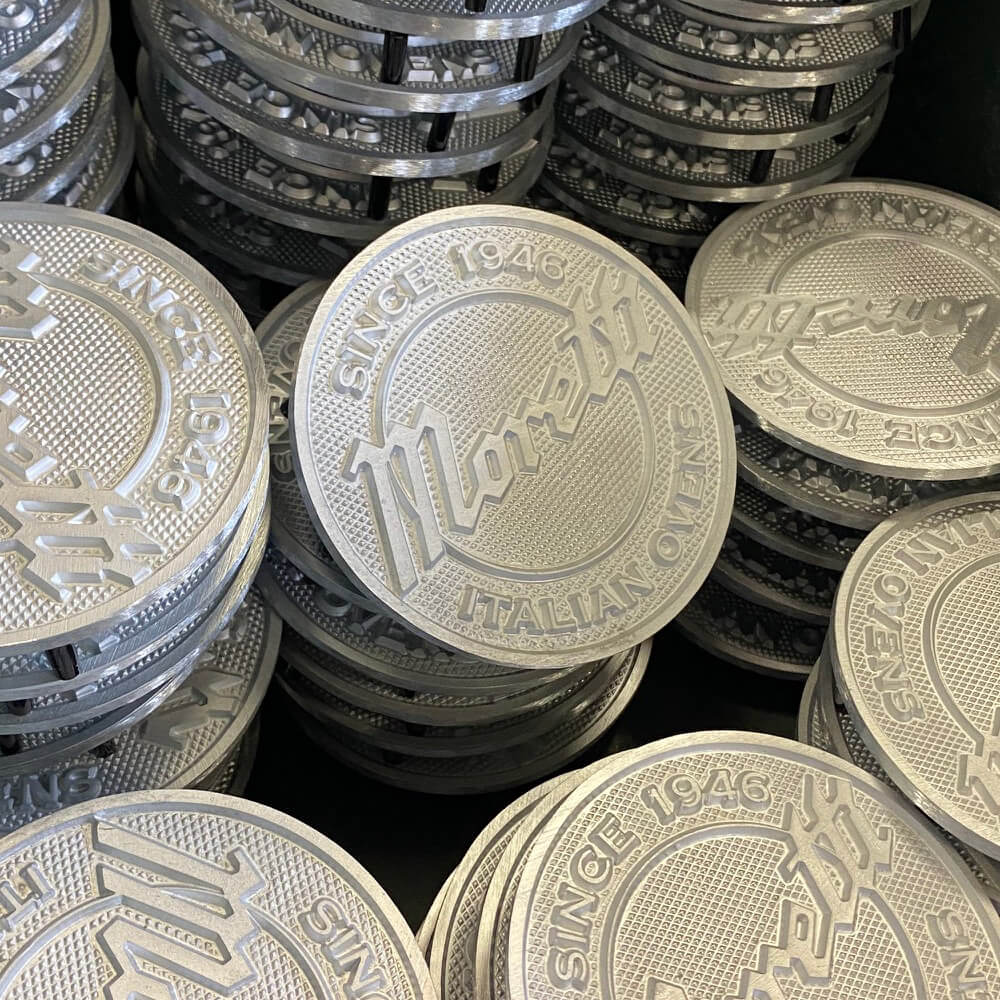
IL PROCESSO
di fusione
La pressofusione viene definita come “un particolare processo di fonderia in forma permanente, in cui metallo fuso viene iniettato ad alta pressione in uno stampo”.
Tutto parte dalla creazione dello stampo utilizzando una gomma siliconica. Nello specifico, questo stampo viene intagliato, sagomandolo in modo da permettere che la zama fusa possa colarvi all’interno in maniera omogenea ricreando esattamente la tipologia di targhette, o più in generale dell’oggetto particolare di cui abbiamo bisogno.
Pur essendo un ciclo produttivo basato su una fusione, questa è di fatto a basso impatto ambientale. Durante il processo di pressofusione, la zama non disperde nell’ambiente sostanze inquinanti per la sua composizione, essendo una lega di zinco. Inoltre, visto il basso il punto di fusione della zama, consente un notevole risparmio energetico rispetto ad altre tecniche simili di fusione.
Una fase preliminare al processo di fusione, consiste nella creazione di un modello in ottone realizzato a pantografo del tutto identico al prodotto finito, con l’esclusione delle finiture estetiche superficiali, dal quale partire per creare poi lo stampo in gomma che verrà usato per la produzione in serie.
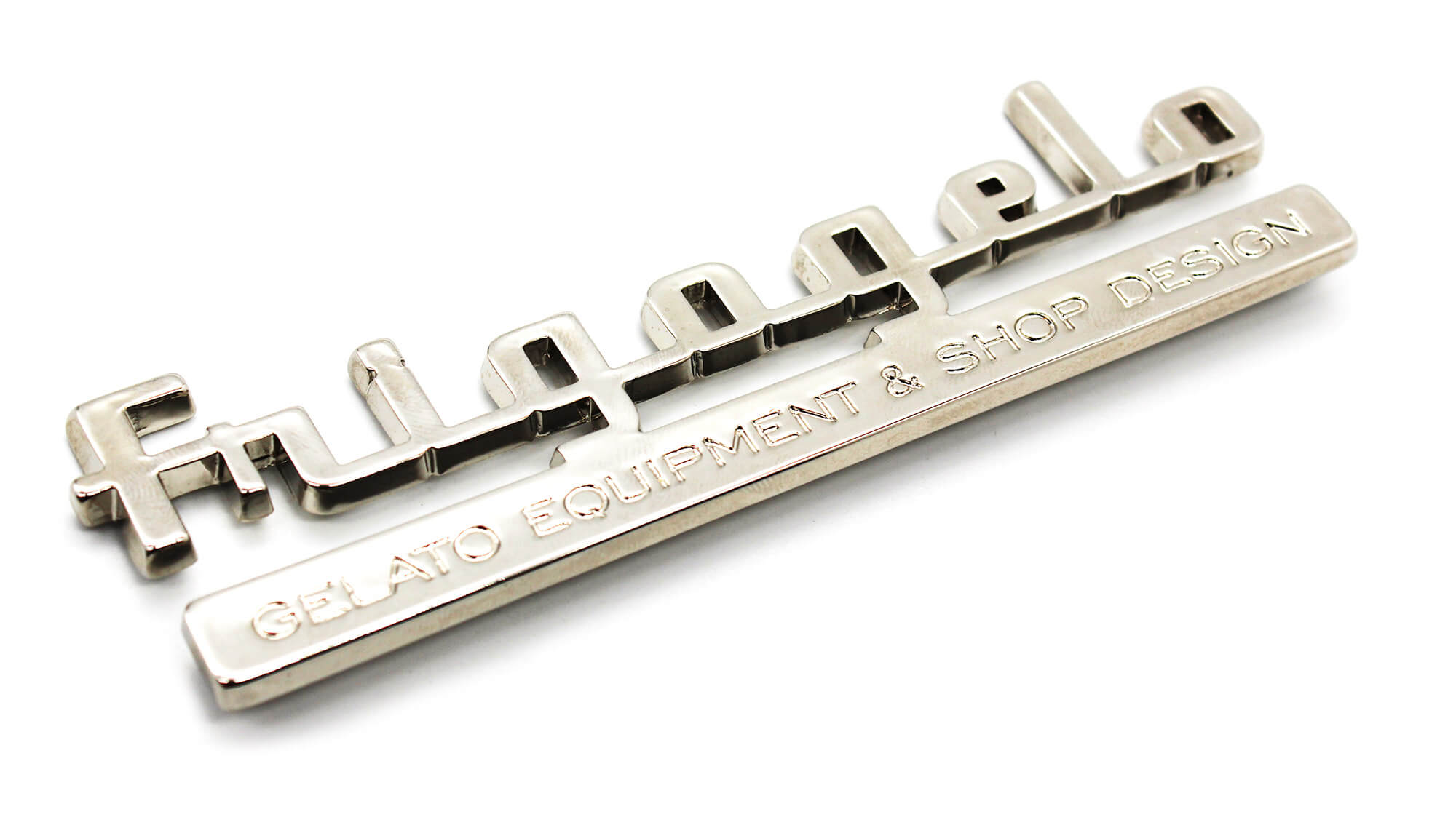
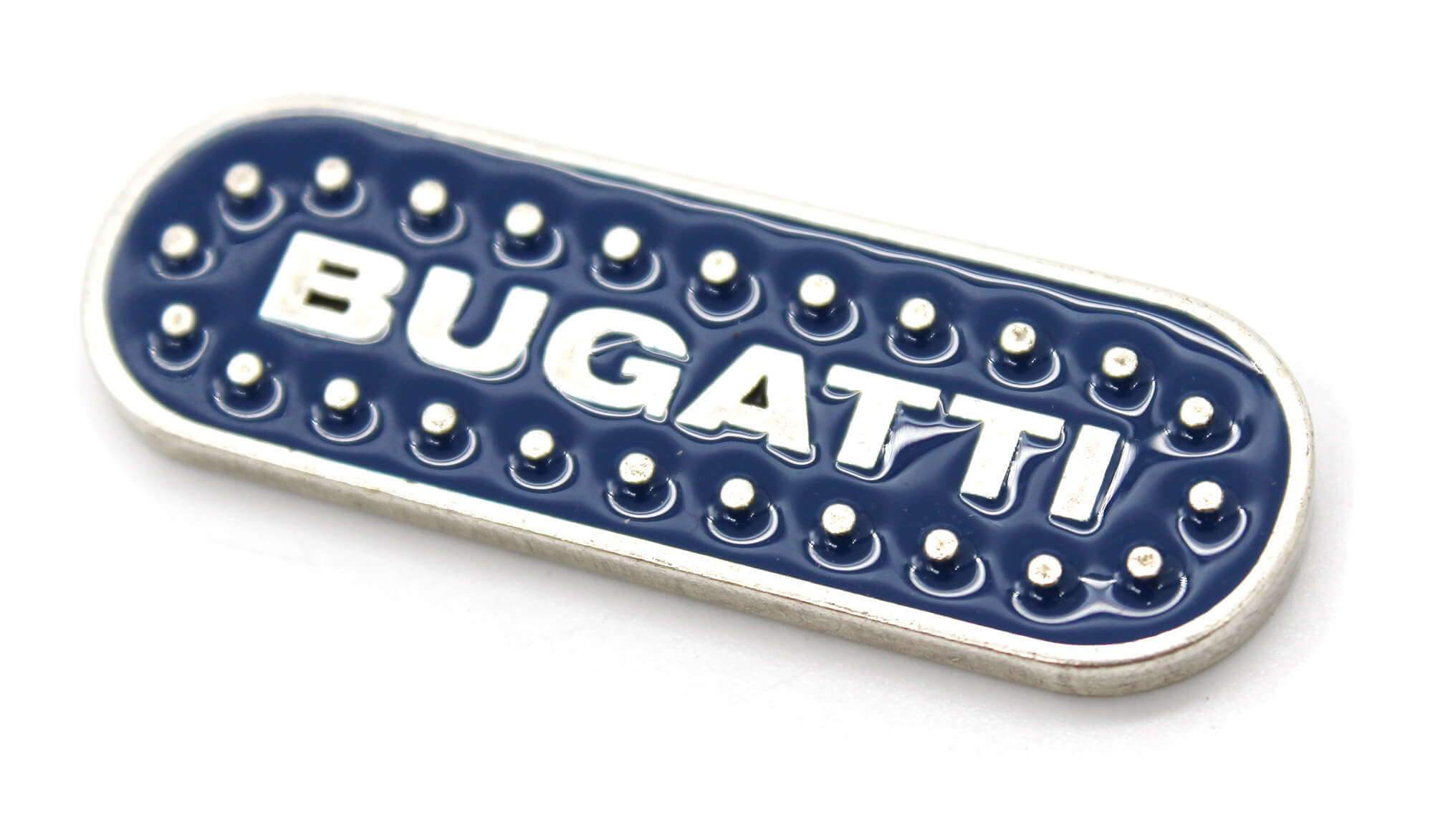
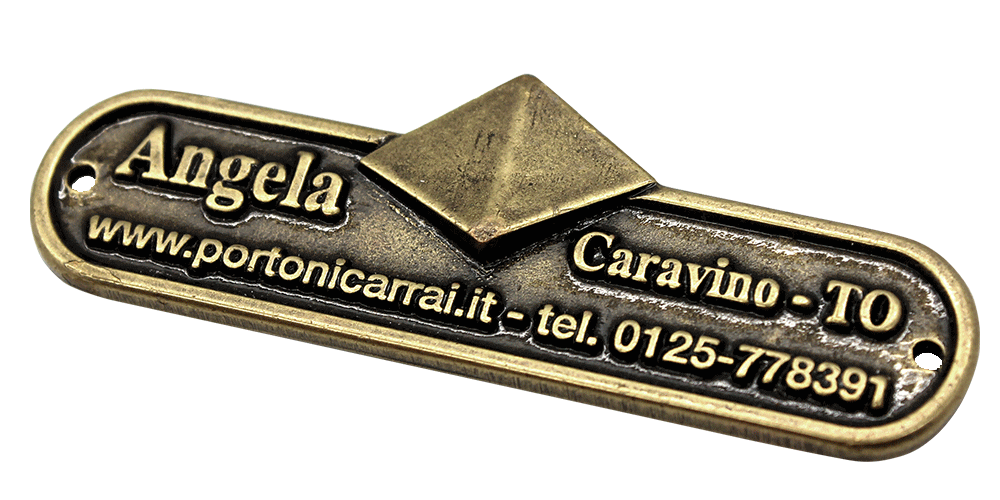
I lingotti di zama vengono fusi ad una temperatura di circa 420 ° C in un forno a circa posto a fianco alla macchina di pressofusione e la lega, una volta raggiunto lo stato liquido, viene iniettata in uno stampo.
Lo stesso materiale che compone lo stampo comporta la scelta della corretta mescola della gomma siliconica. Infatti in base a tutte le particolarità, soprattutto relative agli elementi di rilievo e i vari “livelli” su cui si articola il progetto, va utilizzata la composizione più idonea.
Una volta realizzato lo stampo andremmo a colare il metallo (zama) al suo interno in forma liquida tramite un imbuto di gomma. Da qui raggiunge lo stampo di gomma in rotazione che poi attraverso un’apposita centrifuga distribuirà la materia prima all’interno stampo precedentemente intagliato. Grazie all’elevata fluidità e al basso punto di fusione, la zama permette di ottenere pezzi con limiti di tolleranza molto bassi e, a parità di tempistica, forme complesse e articolate.
Dopo aver raffreddato i singoli pezzi, questi vengono puliti e rifilati per andare a rimuovere i testimoni, prima manualmente in maniera più grossolana, poi rifiniti attraverso la burattatura.
La burattatura consiste nell’aggiunta dei pezzi prodotti all’interno di una vasca vibrante (buratto), per raggiungere determinati effetti superficiali. In base alle polveri abrasive utilizzate possiamo diversamente opacizzare o lucidare, oltre che rimuovere le bave e tutti i residui della fusione su stampo.
GALVANICA
numerose finiture
per esaltare
l’impatto estetico
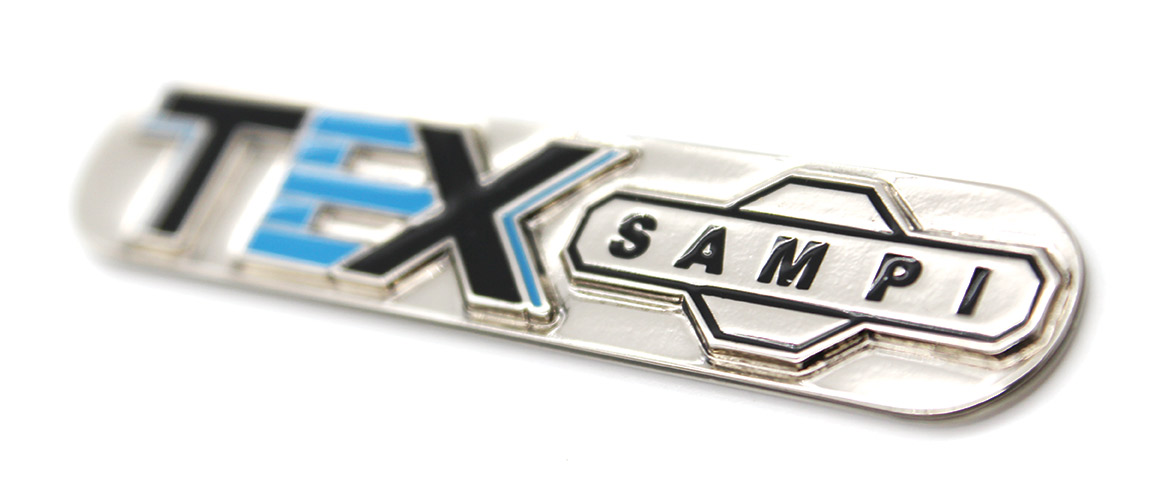
Una volta burattate e accuratamente sgrassate le nostre targhette sono pronte per ricevere il trattamento galvanico. Questo trattamento è composto da processi utilizzati a scopi sia funzionali che estetici, in quanto conferiscono ai metalli su cui vengono effettuati, proprietà importanti come quelle antiabrasiva e anticorrosiva, oltre a conferire durezza e maggiore lucentezza.
Per ottenere un trattamento galvanico si utilizzano bagni comuni con contenuti variabili di differenti metalli in base alla finitura superficiale che si vuole ottenere.
Riportiamo qui di seguito le finiture principalmente richieste:
In base alla differente necessità di precisione e uniformità della finitura superficiale del lotto da produrre si opterà per una galvanica a telaio, per la massima accuratezza disponibile, oppure a rotobarile, per un trattamento leggermente meno uniforme.
Il trattamento di fatto è lo stesso, le uniche differenze sostanziali riguardano il tipo di fissaggio delle targhette che dovranno subire il processo. Nel primo caso saranno appese e fissate con la saldatura di un piccolo testimone, che verrà successivamente rimosso e non comporta alcun difetto estetico poiché trovandosi sul retro della targhetta non sarà visibile. Nel caso in cui le targhette presentino dei fori, verranno sfruttati, evitando quindi il passaggio di saldatura. Con questa tecnica la galvanica rimane perfettamente liscia e aderente alla targa personalizzata.
Diversamente, nel caso della galvanica a rotobarile, le targhette verranno collocate all’interno di barili rotanti che vengono immersi nelle differenti vasche. Conseguenza diretta di questo tipo di lavorazione è che con la rotazione, seppur tenute separate tra loro le targhette urteranno tra loro rendendo la finitura di fondo lievemente meno uniforme. Va da sé che questo tipo di soluzione risulterà più economica rispetto al fissaggio a telaio, quindi nella particolare situazione di lotti produttivi particolarmente elevati spesso è preferita.
Come ultimo passaggio “estetico” si ha la smaltatura, che consiste nell’applicazione di appositi smalti epossidici per riempire gli spazi precedentemente creati con lo stampo per dare colore su specifici elementi della grafica del nostro progetto.
Generalmente la produzione di una targhetta personalizzata giunta a questo punto è pressoché ultimata (rimane solamente l’ultima applicazione del biadesivo di fissaggio, se necessario), ma può capitare di dover fare un ulteriore passaggio di verniciatura per apporre un protettivo lucido o opaco per proteggere la targhetta dagli agenti atmosferici, nel caso di applicazioni outdoor, o dalle alte temperature, nel caso di forni alimentari o industriali.
TARGHE IN PRESSOFUSIONE
applicazioni particolari
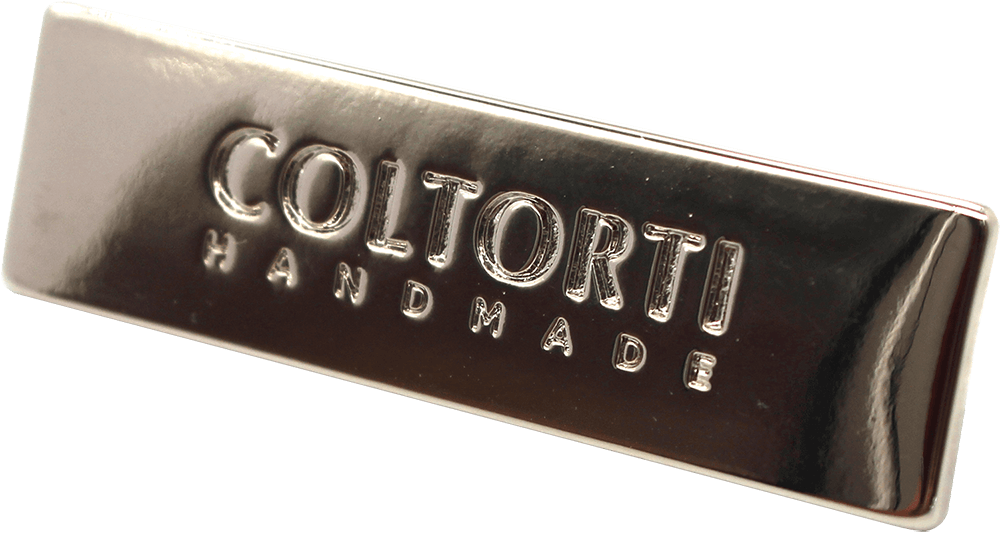
Come già anticipato, questo tipo di processo produttivo ha campi di applicazione molto ampi: dai complementi di abbigliamento (come fibbie e pins, oreficeria in genere) a utilizzi industriali (targhette pressofusione per complementi d’arredo).
Abbiamo citato queste due macro aree specifiche proprio perché in entrambi i casi abbiamo soluzioni di fissaggio particolari.
Nella progettazione di targhette per l’abbigliamento solitamente sul retro dei particolari in zama vengono applicate delle alette pieghevoli che vengono inserite nello stampo in gomma e unito tramite il processo di fusione. La targhetta ottenuta può così essere agevolmente fissata sulla borsa, o qualsiasi altri capo d’abbigliamento si voglia, in maniera molto semplice ma solida allo stesso tempo, evitando la soluzione alternativa più complessa, che sarebbe quella di realizzare una targhetta con dei fori che permettano una successiva cucitura.
Lo stesso vale per le targhe pressofusione che necessitano di chiodini, perni filettati o pioli su retro, nel caso in cui vengano inseriti in supporti preforati. Non essendo un innesto successivo alla creazione della targhetta, questi elementi sono estremamente resistenti, quindi la possibilità che con il tempo queste targhette possano fuoriuscire è molto remota.
Alla luce di tutti questi elementi, possiamo intuire che la pressofusione zama è di fatto un processo produttivo non particolarmente rapido, rispetto ad altre soluzioni tecnologiche proposte dalla nostra azienda; poiché presenta delle tempistiche tecniche che sono difficilmente riducibili.
Non è particolarmente adatta alla prototipazione, se non in fase già avanzata, poiché va necessariamente realizzato uno stampo per poter procedere con la lavorazione. Va da se che qualsiasi modifica che non riguardi finiture, o colori, necessita la creazione di un nuovo stampo.
Quindi è un’ottima soluzione sia in termini tecnici che economici nel caso di lotti produttivi numerosi, ma è sconsigliata per pochi pezzi.
Nel caso in cui vogliate realizzare delle targhette in pressofusione, ma non si hanno le idee chiare, siamo a vostra completa disposizione per studiare insieme la migliore soluzione possibile per le vostre esigenze!
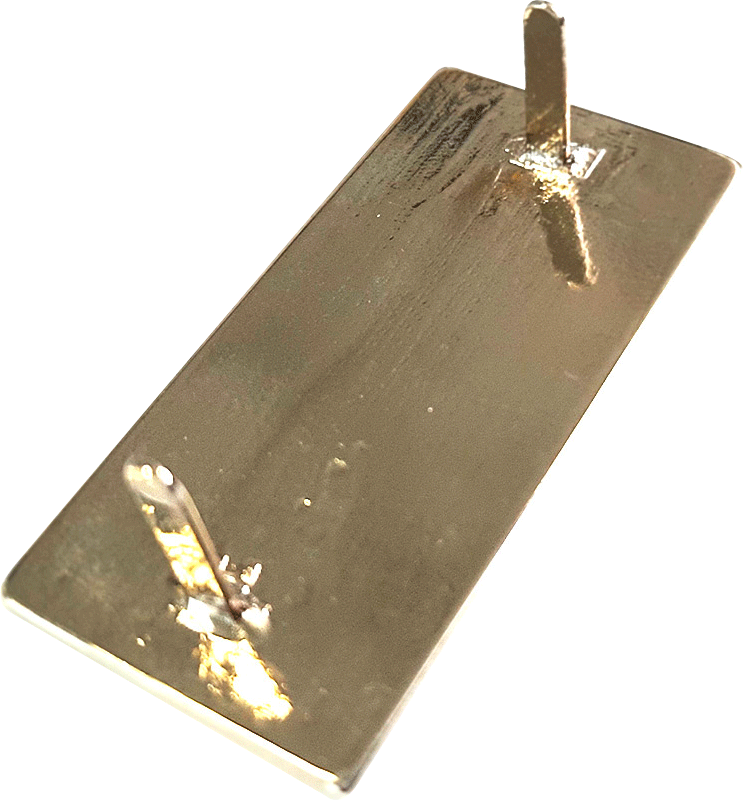